What is Porosity in Welding: Ideal Practices for Staying Clear Of Permeable Welds
Comprehending Porosity in Welding: Checking Out Reasons, Impacts, and Prevention Strategies
As experts in the welding market are well conscious, understanding the reasons, results, and avoidance methods associated to porosity is vital for attaining robust and trusted welds. By delving into the origin creates of porosity, analyzing its harmful effects on weld high quality, and checking out efficient avoidance approaches, welders can boost their knowledge and abilities to create high-quality welds consistently.
Common Reasons For Porosity
Contamination, in the type of dust, grease, or corrosion on the welding surface, creates gas pockets when heated, leading to porosity in the weld. Improper shielding takes place when the securing gas, commonly made use of in processes like MIG and TIG welding, is incapable to completely protect the liquified weld swimming pool from reacting with the bordering air, resulting in gas entrapment and succeeding porosity. Furthermore, poor gas coverage, commonly due to incorrect flow prices or nozzle positioning, can leave parts of the weld vulnerable, permitting porosity to form.
Results on Weld High Quality
The existence of porosity in a weld can dramatically endanger the total high quality and stability of the welded joint. Porosity within a weld produces spaces or cavities that weaken the structure, making it more susceptible to cracking, deterioration, and mechanical failing.
In addition, porosity can prevent the efficiency of non-destructive testing (NDT) techniques, making it testing to detect various other flaws or discontinuities within the weld. This can bring about considerable safety concerns, particularly in important applications where the architectural integrity of the welded parts is extremely important.

Prevention Techniques Summary
Given the detrimental impact of porosity on weld top quality, reliable avoidance methods are important to preserving the architectural honesty of welded joints. Furthermore, selecting the ideal welding parameters, such as voltage, existing, and take a trip rate, can help lessen the danger of porosity development. By including these prevention methods into welding practices, the event of porosity can be substantially decreased, leading to more powerful and more reliable bonded joints.
Significance of Correct Shielding
Proper protecting in welding plays an important role in protecting against atmospheric contamination and ensuring the integrity of welded joints. Securing gases, such as argon, helium, or a mix of both, are generally used to shield the weld pool from responding with elements in the air like oxygen and nitrogen. When these responsive components enter into call with the hot weld pool, they can create porosity, causing weak welds with decreased mechanical homes.
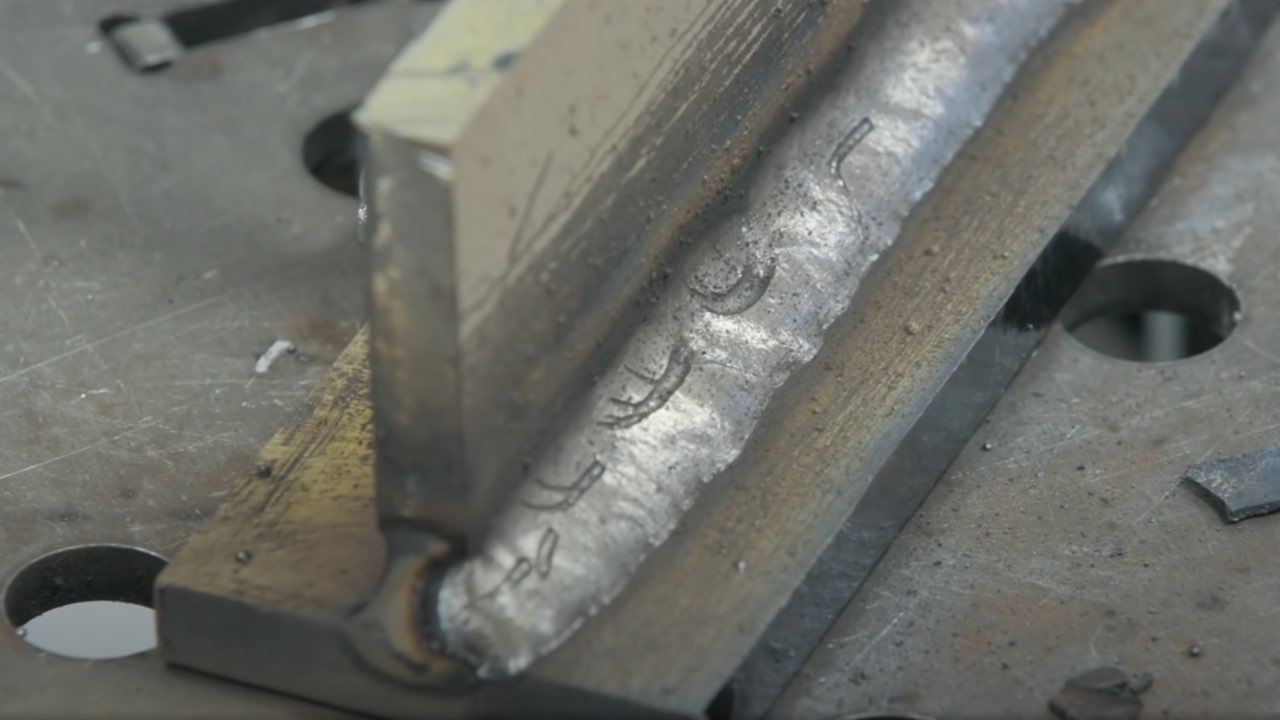
Insufficient protecting can lead to different flaws like porosity, spatter, and oxidation, compromising the structural integrity of the bonded joint. Sticking to correct protecting methods is vital to produce high-quality welds with minimal defects and make certain the durability and reliability of the bonded elements.
Monitoring and Control Techniques
How can welders properly keep track of and manage the welding procedure to ensure optimal outcomes and avoid flaws like porosity? By continually keeping track of these variables, welders can determine deviations from the excellent conditions and make immediate modifications to stop porosity you can look here development.

Additionally, applying correct training programs for welders is important for keeping track of and managing the welding process successfully. What is Porosity. Informing welders on the importance of maintaining constant criteria, such as appropriate gas protecting and travel speed, can help avoid porosity issues. Regular assessments and accreditations can also guarantee that welders excel in monitoring and controlling welding processes
Furthermore, using automated welding systems can boost surveillance and control capabilities. These systems can precisely manage welding criteria, look at this site minimizing the probability of human mistake and making certain consistent weld top quality. By integrating sophisticated monitoring technologies, training programs, and automated systems, welders can efficiently monitor and regulate the welding process to minimize porosity issues and achieve top quality welds.
Conclusion
